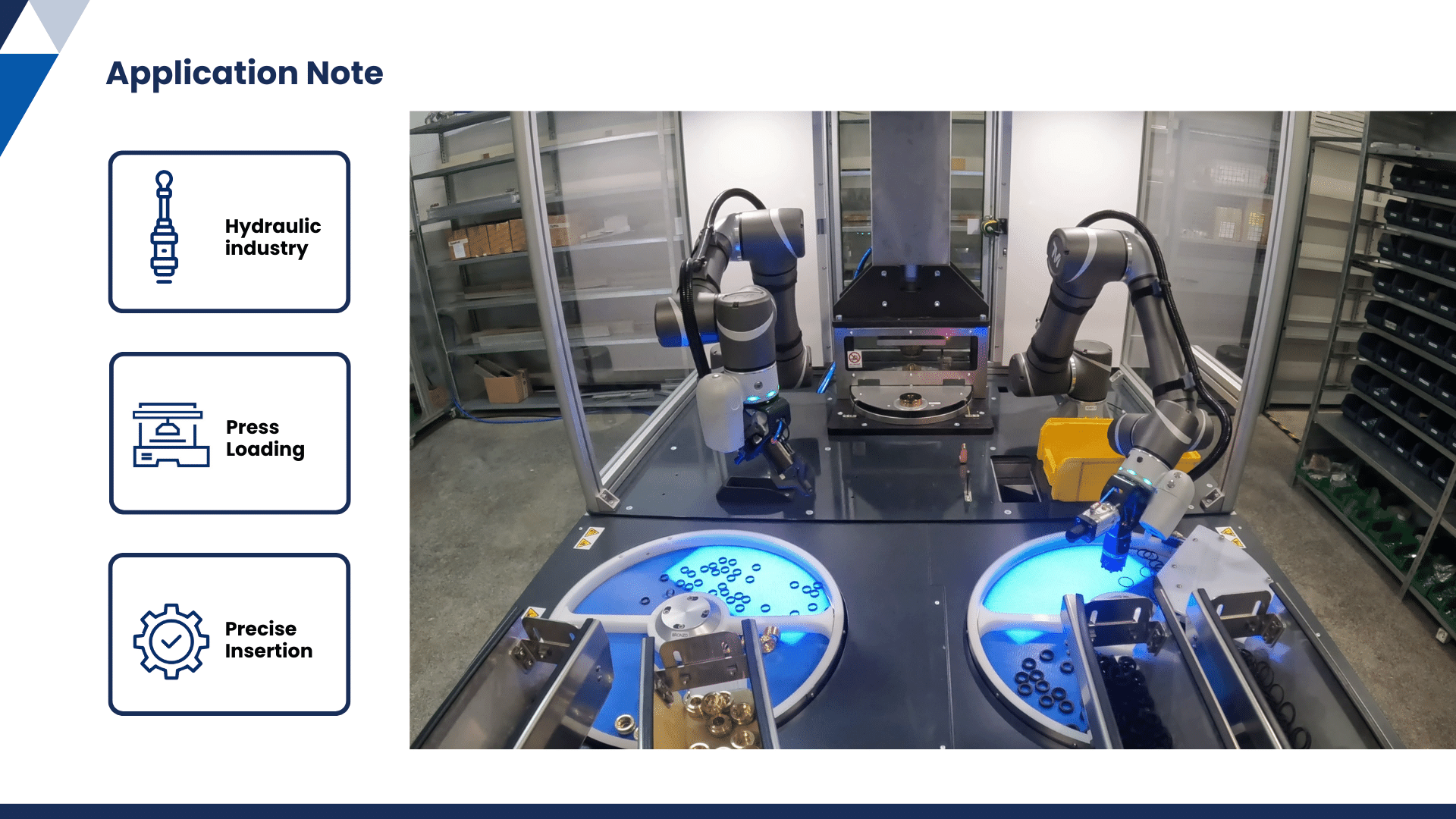
Enhancing Press Loading for Hydraulic Component Production through Efficient Part Feeding
Case study: a flexible feeding solution applied to a hydraulic press loading.
Our partner
Ergonit's mission is to offer automated and customized solutions that help customers increase the efficiency of their production processes, reducing time and costs, by providing the best possible control over production phases and optimizing the resources used.
The Challenge
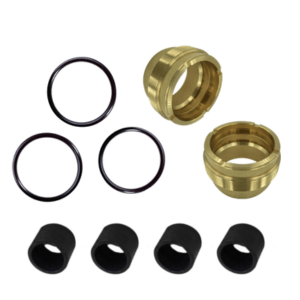
- 4 parts to be handled simultaneously.
- Manage different components varying in shape and material within a compact layout.
- Implement rigorous quality controls and high precision assembly.
- Need for a flexible feeder compatible with collaborative robots.
The Solution
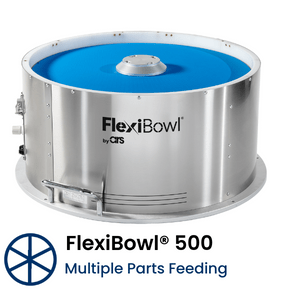
- Two FlexiBowl® 500 feeders equipped with a 2-sector disc, for the simultaneous feeding of different metal components.
- Two Techman Robot cobots, each equipped with an integrated camera and a dual End-of-Arm Tooling (EOAT) system.
The Benefit
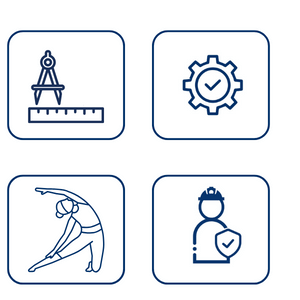
- Compact layout seamlessly handles diverse components within a stringent quality control framework
- Exceptional precision and a significantly reduced error rate for a reliable and efficient production process.
- A flexible feeding solution to quickly adapt to different material and geometry such as o-rings, bronze and graphite parts.
- Thanks to collaborative robots and the FlexiBowl feeder, the manufacturing process is now more secure and monitored.
Abstract
Ergonit developed a highly flexible and precise production system for Interpump Spa's hydraulic components assembly. The solution involved a robotic island equipped with two FlexiBowl®500 feeders and two Techman Robot cobots.
Designed for a compact layout, the system efficiently managed several different components of varying shape, size, and material. The integration of an infinite recipe memory feature at the software level of the FlexiBowl® system, along with the use of integrated camera and dual EOAT systems on the cobots, ensured precise handling, high-quality assembly checks, and easy adaptability to different components. This system significantly reduced the error rate and enhanced the production process's efficiency, all while maintaining rigorous quality control standards - setting the stage for future business developments and adaptations.