Introduction: The Global Medical Sector
The global medical sector, with its continuous advancements and technological innovations, plays a pivotal role in improving the quality of life and reducing mortality worldwide. The industry faces unique challenges like rapid changes in manufacturing environments and design decisions, strict regulatory audits, and the need for reduced time to market to maintain competitiveness.
The Evolving Landscape: Technological Innovations and Production Challenges
In the medical sector, the need for flexibility, modularity, and the ability to adapt quickly to changes is critical. Hard automation equipment struggles in this dynamic environment. However, solutions like FlexiBowl, with its patented technology, offer much-needed adaptability and efficiency, making it a vital tool for advanced manufacturing processes in the medical industry.
Embracing Industry 4.0: The Shift Towards Flexible Part Feeding
With the rise of Industry 4.0 technologies, medical device manufacturers are under increasing pressure to adapt their production lines. At the center of this transformation is flexible part feeding, a method that allows for greater adaptability in handling a diverse array of medical components.
FlexiBowl® Certified
The versions of Flexibowl® certified for use in ISO Class 5 controlled environments as defined by ISO 14644-1 maintain all the functions of the standard FlexiBowl®. Main features:
- Pneumatic components specific for cleanroom use;
- Back-lighted glass plate
- Perforated top screen to favor laminar flow
- Available for FlexiBowl® 350/500/650/800 feeding systems
- Product contact surface suitable for cleanroom use
- Cap in natural white polyethylene to prevent component jams at center
Ready to find out more?
Drop us a line today for a free quote!
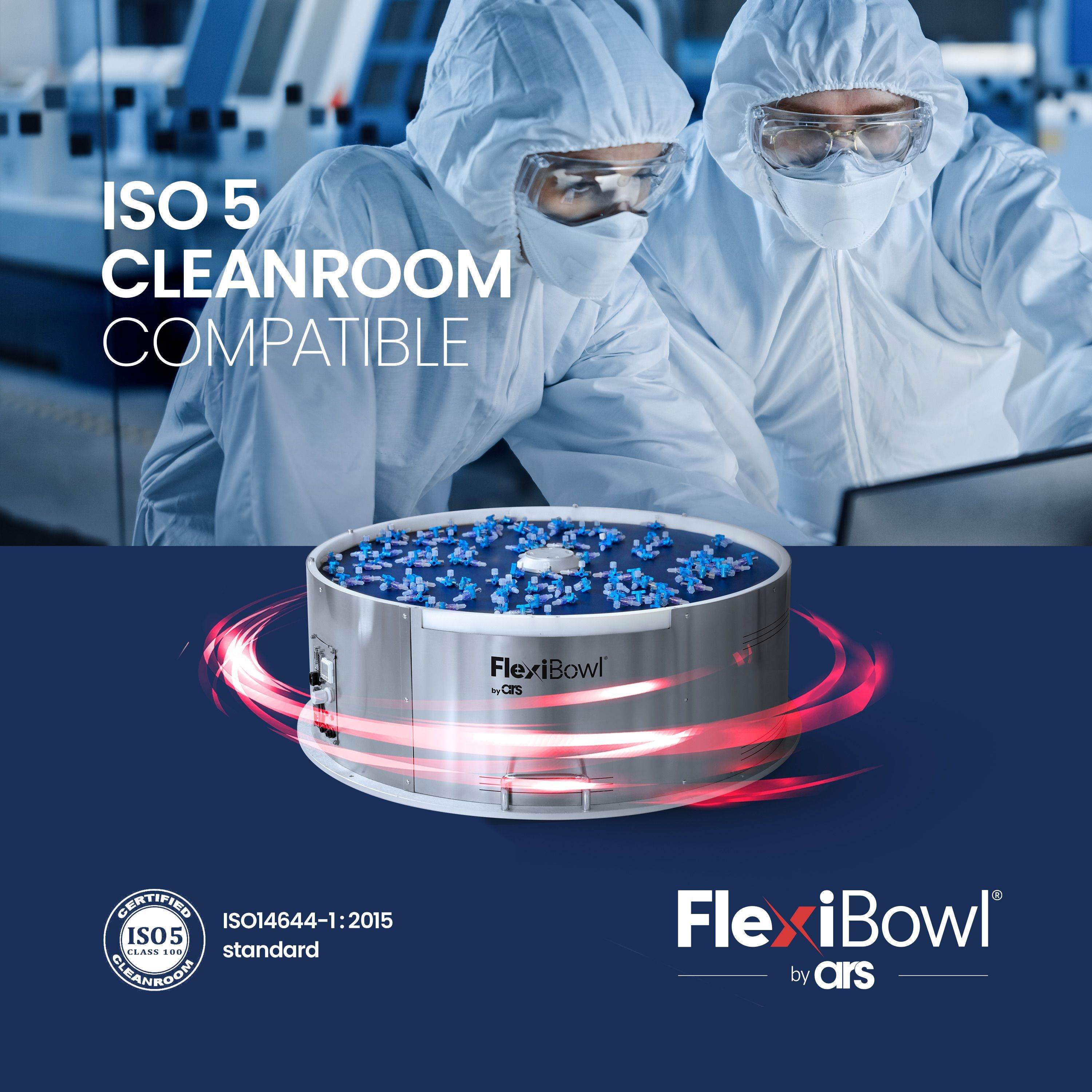
Cylindrical
Complex
Flat
Medical Parts Feeder: The Case of FlexiBowl®
FlexiBowl® serves as a leading example of a medical parts feeder, offering multiple advantages such as:
- Versatility: FlexiBowl® can handle a variety of part shapes, sizes, and materials, eliminating the need for multiple feeders.
- Increased Efficiency: By reducing downtime due to feeder changeovers, FlexiBowl®'s technology increases production speed.
- Adaptability: It allows for rapid and smooth transitions between different parts, enhancing overall workflow.
A flexible feeder like FlexiBowl® can be implemented in various production processes, particularly when dealing with components of varying sizes.
- Medical Device Assembly: During the assembly of medical devices or subsystems, FlexiBowl® can supply parts of varying sizes to the assembly line, readily adjusting its operation based on the size of the component being handled.
- Quality Control: FlexiBowl® can be used to present components to inspection devices, such as machine vision systems or sensors, ensuring accurate inspection and reliable quality control.
- Disposable Product Production: FlexiBowl® can handle the production of disposable items, like syringes, needles, bandages, gloves, and more. Its ability to handle a variety of shapes, sizes, and materials makes it ideal for this type of production.
- Packaging: In medical device packaging processes, a flexible feeder like FlexiBowl® can simplify and expedite the process of placing components into packaging.
- Electronic Component Production: The manufacturing of electronic components for medical devices can benefit from the use of FlexiBowl®. It can handle delicate and small-sized components like integrated circuits, connectors, switches, relays, and fuses.
Remember, integrating FlexiBowl® into production processes can increase efficiency, reduce downtime, and improve the flexibility of the production process.
Flexible Part Feeding: The Advantages of FlexiBowl®
FlexiBowl®, a pioneering solution in flexible part feeding technology, stands out for its multiple benefits, including:
- Ease of Integration: Designed to seamlessly fit into any production project, FlexiBowl® makes its incorporation into existing systems straightforward and efficient.
- Production Flexibility: The system allows for easy adaptation to any production changes, reflecting its innate flexibility and adaptability.
- Accurate Part Recognition and Orientation: FlexiBowl® ensures precise recognition and positioning of various components, boosting overall productivity and minimizing errors.
Types of Components a Medical Parts Feeder Can Handle
- Delicate and Small-Sized Components: FlexiBowl® is suited for handling delicate and/or small-sized components.
- Closures: FlexiBowl® can handle closures such as screw caps, spouted caps, pump and pressure caps, pipettes, droppers, diffusers, roll-ons, seals, discs, and inserts (pourers, droppers, etc.).
- Containers: FlexiBowl® is capable of dealing with containers such as vials, bottles, and jars.
- Syringes: FlexiBowl® can handle components like plunger rods and backstops; plungers, sealing rings, needles, pistons, dispensers.
- Test and Swab Components: FlexiBowl® is adept at handling components used for tests and swabs.
- Complex Geometries and Material Types: Unlike traditional vibrating bowl feeders, flexible systems like FlexiBowl® gently handle parts, managing complex geometries and different types of materials, and reducing the risk of unwanted damage.
- Small Parts: Complex geometrical parts, delicate materials, and sophisticated electronic components that are characteristic of today's medical devices.
- ISO Class 5 Compatibility: FlexiBowl® is compatible to operate in environments up to Class ISO 5 according to the EN ISO-14644-1 standard.
Embracing the Future of Medical Production using a perfect Medical Parts Feeder
The future success of the medical industry depends on its ability to adapt, innovate, and respond to the evolving production landscape. Here, flexible part feeding technologies like FlexiBowl® are set to play a pivotal role, aiding in the rapid production of medical devices and helping cater to a globally aging population and the growing demand for healthcare services.
Videos

103 x 21 mm

147 x 5 mm
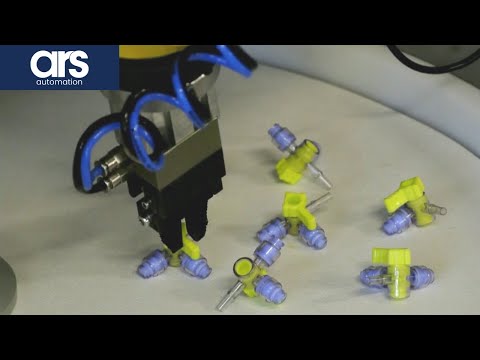
42 x 24 mm

60 x 28 mm
Why should you invest in a FlexiBowl feeding unit?
Its lack of dedicated tooling and its easy-to-use and intuitive programming allows quick and multiple product changeovers inside the same work shift.
FlexiBowl® solution is highly versatile and is able to feed parts with every:
- Geometry
- Surface
- Material
Its rotary disc are FDA certified and keep antistatic filaments that prevents accumulation of electrical charges on its surface, suitable for electric components. Thanks to its unique working principle provides the best feed-rate in its category.
Challenge the various applications it may be applied in your manufacturing operations!
Main end users
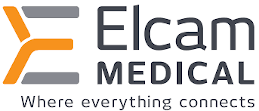
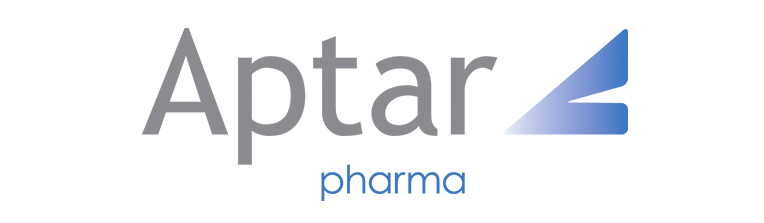
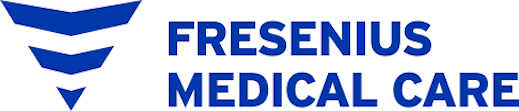
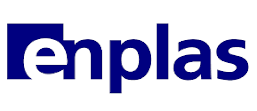
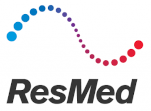
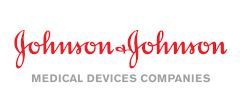